En un reciente LinkedIn blog, detallé cuatro preguntas que, una vez respondidas, revelarán cómo se realizan los pronósticos. siendo utilizado en tu negocio En este artículo, hemos enumerado preguntas que puede hacer que revelarán cómo se realizan los pronósticos. creado.
1. Cuando preguntamos a los usuarios cómo crean pronósticos, su respuesta suele ser "usamos el historial". Obviamente, esto no es suficiente información, ya que existen diferentes tipos de historial de demanda que requieren diferentes métodos de pronóstico. Si está utilizando datos históricos, asegúrese de averiguar si está utilizando un modelo promedio, un modelo de tendencias, un modelo estacional o algo más para pronosticar.
2. Una vez que sepa el modelo utilizado, pregunte acerca de los valores de los parámetros de esos modelos. El resultado del pronóstico de un "promedio" diferirá, a veces significativamente, según la cantidad de períodos que esté promediando. Entonces, averigüe si está usando un promedio de los últimos 3 meses, 6 meses, 12 meses, etc.
3. Si está utilizando modelos de tendencia, pregunte cómo se establecen los pesos del modelo. Por ejemplo, en un modelo de tendencias, como el suavizado exponencial doble, los pronósticos diferirán significativamente según cómo los cálculos ponderen los datos recientes en comparación con los datos más antiguos (las ponderaciones más altas ponen más énfasis en los datos recientes).
4. Si está utilizando modelos estacionales, los resultados del pronóstico se verán afectados por el "nivel" y las "ponderaciones de tendencia" utilizadas. También debe determinar si los períodos estacionales se pronostican con estacionalidad multiplicativa o aditiva. (La estacionalidad aditiva dice, por ejemplo, "Suma 100 unidades para julio", mientras que la estacionalidad multiplicativa dice "Multiplica por 1,25 para julio"). Finalmente, es posible que no estés usando este tipo de métodos en absoluto. Algunos profesionales utilizarán un método de pronóstico que simplemente promedia períodos anteriores (es decir, el próximo mes de junio se pronosticará con base en el promedio de los tres junios anteriores).
5. ¿Cómo haces para elegir un modelo sobre otro? ¿Depende la elección de la técnica del tipo de datos de demanda o de la disponibilidad de nuevos datos de demanda? ¿Este proceso está automatizado? O si un planificador elige subjetivamente un modelo de tendencia, ¿se seguirá pronosticando ese elemento con ese modelo hasta que el planificador lo cambie de nuevo?
6. ¿Son sus pronósticos “totalmente automáticos”, de modo que la tendencia y/o la estacionalidad se detecten automáticamente? ¿O sus pronósticos dependen de las clasificaciones de artículos que deben mantener los usuarios? Este último requiere más tiempo y atención por parte de los planificadores para definir qué comportamiento constituye tendencia, estacionalidad, etc.
7. ¿Cuáles son las reglas de clasificación de artículos que se utilizan? Por ejemplo, un artículo puede considerarse un artículo de tendencia si la demanda aumenta más de 5% período tras período. Un artículo puede considerarse estacional si el 70% o más de la demanda anual ocurre en cuatro períodos o menos. Tales reglas están definidas por el usuario y, a menudo, requieren suposiciones demasiado amplias. A veces, se configuran cuando un sistema se implementó originalmente, pero nunca se revisó, incluso cuando cambian las condiciones. Es importante asegurarse de que se comprendan las reglas de clasificación y, si es necesario, se actualicen.
8. ¿El pronóstico se regenera automáticamente cuando hay nuevos datos disponibles o tiene que regenerar manualmente los pronósticos?
9. ¿Revisa si hay algún cambio en el pronóstico de un período al siguiente antes de decidir si usa el nuevo pronóstico? ¿O prefieres el nuevo pronóstico por defecto?
10. ¿Cómo se tratan las anulaciones de pronóstico que se realizaron en ciclos de planificación anteriores cuando se crea un nuevo pronóstico? ¿Se reutilizan o se reemplazan?
11. ¿Cómo incorpora las previsiones realizadas por su equipo de ventas o por sus clientes? ¿Estos pronósticos reemplazan el pronóstico de línea base o utiliza estas entradas para hacer anulaciones del planificador al pronóstico de línea base?
12. ¿Bajo qué circunstancias ignoraría el pronóstico de referencia y usaría exactamente lo que le dicen las ventas o los clientes?
13. Si confía en los pronósticos de los clientes, ¿qué hace con los clientes que no brindan pronósticos?
14. ¿Cómo documenta la efectividad de su enfoque de pronóstico? La mayoría de las empresas solo miden la precisión del pronóstico final que se envía al sistema ERP, si es que miden algo. Pero no evalúan predicciones alternativas que podrían haberse utilizado. Es importante comparar lo que está haciendo con los puntos de referencia. Por ejemplo, ¿los métodos que está utilizando superan un pronóstico ingenuo (es decir, "mañana es igual a hoy", que no requiere pensar), o lo que vio el año pasado, o el promedio de los últimos 12 meses? La evaluación comparativa de su pronóstico de referencia asegura que está exprimiendo la mayor precisión posible de los datos.
15. ¿Mide si las anulaciones de ventas, clientes y planificadores mejoran o empeoran el pronóstico? Esto es tan importante como medir si sus enfoques estadísticos están superando al método ingenuo. Si no sabe si las anulaciones están ayudando o perjudicando, la empresa no puede mejorar en la previsión; necesita saber qué pasos están agregando valor para que pueda hacer más y mejorar aún más. Si no está documentando la precisión del pronóstico y realizando un análisis de "valor agregado del pronóstico", entonces no podrá evaluar adecuadamente si los pronósticos que se producen son los mejores que podría hacer. Perderá oportunidades para mejorar el proceso, aumentar la precisión y educar a la empresa sobre qué tipo de error de pronóstico se espera.
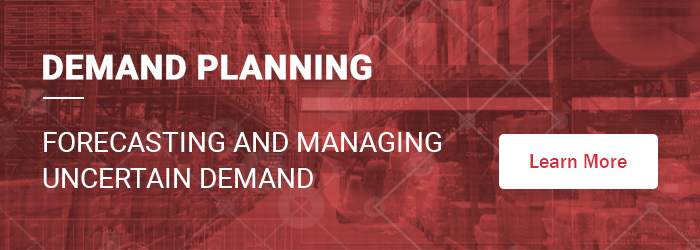