Los parámetros de planificación del inventario, como los niveles de existencias de seguridad, los puntos de pedido, la configuración mínima/máxima, los plazos de entrega, las cantidades de los pedidos y los búferes de DDMRP afectan directamente los gastos de inventario y la capacidad para satisfacer la demanda de los clientes. En función de la configuración de estos parámetros, su sistema ERP realiza sugerencias de órdenes de compra diarias.
Asegurarse de que estas entradas se entiendan y optimicen regularmente reducirá sustancialmente el gasto de inventario innecesario y mejorará drásticamente los niveles de servicio al cliente.
Dada la importancia de acertar con estos parámetros de planificación, pasamos mucho tiempo durante nuestras consultas preguntando (1) cómo se calculan estos valores de parámetros y (2) con qué frecuencia se actualizan. La mayoría de las veces, los métodos para calcular los valores de los parámetros son la regla general. Puede leer acerca de por qué el uso de enfoques de regla empírica es tan problemático aquí: Tenga cuidado con las reglas generales simples para administrar el inventario.
Este blog se centrará en la frecuencia de las actualizaciones. Cuando entrevistamos a empresas y les preguntamos con qué frecuencia actualizan los parámetros de planificación, la respuesta que casi siempre escuchamos es "¡todos los días!" Una o dos preguntas de seguimiento suelen revelar que esto no es cierto. Lo que “todos los días” realmente significa en la práctica es esto: todos los días, el sistema ERP sugiere de docenas a cientos de órdenes de compra y/o trabajos de producción. El planificador, llamémosle Peter, revisa estos pedidos diariamente y decide si liberarlos, modificarlos o cancelarlos. Si la sugerencia de pedido no se siente bien, Peter revisa las entradas de planificación y modifica el pedido si es necesario. Por ejemplo, Peter puede sentir que ya hay suficiente inventario disponible. Para "arreglar" el problema, reducirá el punto de pedido y cancelará el pedido. O si siente que el pedido debería haberse realizado hace semanas, Peter puede acelerar el pedido y aumentar el punto de pedido y la cantidad del pedido para asegurarse de que haya suficientes existencias la próxima vez.
Los principales defectos de este enfoque son que es reactivo e incompleto. He aquí por qué:
Reactivo
Solo evalúa el puñado de artículos marcados para reposición en un día determinado, pero no en otros. El desencadenante para revisar un artículo es cuando el ERP sugiere un pedido, y eso solo sucederá cuando se incumpla el punto de reorden o Min. Si el Min es demasiado alto y se incumple antes de lo que debería, se realizará un pedido innecesario a menos que el planificador lo detecte. Si el Min es demasiado bajo, bueno, es demasiado tarde para corregir el error. No importa qué tan grande sea la sugerencia de pedido, todavía tiene que esperar para que se le reabastezca y, dado que el pedido se sugirió tarde, es muy probable que se agote el stock durante el período de reabastecimiento. ¿Dónde está la “planificación” en tal proceso? Como dijo un cliente: "Nuestro proceso anterior, en retrospectiva, se dedicaba a administrar los resultados y no los insumos".
Incompleto
¿Qué pasa con los miles de otros artículos que tienen un Mín./Máx., Stock de seguridad, Punto de pedido u otros parámetros que no se están reevaluando dados los datos actualizados de oferta y demanda? El planificador no está revisando ninguno de estos elementos, lo que significa que los problemas no se identifican de antemano. Para agravar el problema, cuando Peter hace un cambio, no tiene ninguna herramienta para evaluar la calidad de sus cambios. Si modifica la configuración mínima/máxima, no sabe el impacto específico que esto tendrá en el valor del inventario, los costos de pedido, los costos de mantenimiento, las roturas de existencias y los niveles de servicio. Solo sabe que un aumento en el inventario probablemente mejorará el servicio y aumentará los costos. No sabe, por ejemplo, si su inventario ha llegado a un punto de Rendimientos decrecientes. Cuando las decisiones de inventario se toman con solo una comprensión muy aproximada de las compensaciones, se crean más problemas aguas abajo. No le gustaría que su carpintero hiciera estimaciones aproximadas de sus medidas, pero es común que los profesionales de planificación de inventario lo hagan con millones de dólares en gastos de inventario en juego.
¿Con qué frecuencia la mayoría de las empresas actualizan los parámetros?
Entonces, ¿con qué frecuencia la mayoría de las empresas realizan actualizaciones en todo el sistema de sus parámetros de planificación, como puntos de pedido, existencias de seguridad, configuraciones mínimas/máximas, plazos de entrega y cantidades de pedidos? Por lo general, las actualizaciones masivas ocurren trimestralmente, anualmente y, en algunos casos, nunca; las únicas veces que se realizan cambios es cuando ERP activa un pedido. No es exactamente ágil.
La principal razón que se da para no intervenir más a menudo es que lleva demasiado tiempo. La mayoría de las empresas establecen estos parámetros clave utilizando programas de Excel muy difíciles de manejar o aplicaciones ERP que simplemente no están diseñadas para llevar a cabo una planificación de inventario sistémica. Aquí es donde el software de optimización de inventario puede ayudar.
Uso de software de optimización de inventario y pronóstico de probabilidad actualizar los parámetros clave de planificación con frecuencia, digamos cada semana o mes en lugar de trimestral o anualmente, le permite responder rápidamente a los cambios en su negocio. Puede aprovechar las oportunidades de ahorro de costos, como cuando baja la demanda y puede reducir los puntos de pedido y/o las cantidades de los pedidos y posiblemente cancelar los pedidos pendientes. O puede responder a los problemas, como cuando los aumentos de la demanda amenazan sus compromisos de nivel de servicio con los clientes, o los plazos de entrega de los proveedores aumentan y requieren volver a calcular los puntos de pedido.
Cómo hacerlo bien
La clave es establecer un conjunto acordado de métricas de rendimiento y valor de inventario y permitir que el software controle el estado del juego en segundo plano y lo alerte sobre situaciones excepcionales. Esta es simplemente una forma más de decir que, una vez que se han establecido los sistemas, desea seguir adelante con la administración por excepción. Puede establecer rangos dentro de los cuales las cosas pueden fluir como lo hacen normalmente, pero una vez que un parámetro crítico como "riesgo de agotamiento de existencias excede un nivel predefinido" o "valor de inventario o costos exceden un nivel predefinido", el software puede proporcionar una alerta diaria y también puede recomendar una respuesta, como aumentar un punto de pedido. Con este nivel de asistencia automatizada, es posible mantenerse al tanto del inventario sin sentirse abrumado por el gran volumen de datos.
Por ejemplo, puede elegir un conjunto inicial de parámetros de inventario como política porque podría ver en el software que cumple con sus objetivos de nivel de servicio dentro de su presupuesto de inventario. Puede dejar que el sistema le prescriba objetivos de nivel de servicio y sentirse cómodo con la configuración porque el valor del inventario está dentro del presupuesto. Sin embargo, si la demanda se vuelve menos predecible que históricamente, no podrá lograr el mismo nivel de servicio sin un aumento en el inventario. Un informe de excepción identificará esto y le permitirá tomar una decisión informada sobre qué hacer. Puede decidir modificar la política o mantenerla igual. Si lo mantiene igual, ahora conoce los riesgos adicionales y el cambio en los costos de inventario. Esto se puede comunicar a todos los interesados para que no haya sorpresas.
Planifique, no reaccione
En lugar de estar constantemente en modo reactivo, puede manejar lo que realmente necesita ser manejado y todavía tener algo de tiempo para pensar en el futuro. Por ejemplo, puede realizar análisis hipotéticos sobre cuestiones tales como qué plazos de entrega del proveedor producirían la mayor rentabilidad si se redujeran, o si los objetivos de nivel de servicio deberían ajustarse para tener en cuenta los cambios en la criticidad del cliente o cuestiones de política similares. Después de todo, no es que no vaya a terminar con una agenda diaria completa, es solo una cuestión de si puede elevar esa agenda a un nivel más estratégico. Entonces, si está gastando todo su tiempo de "planificación" administrando los resultados de su ERP en lugar de revisar y optimizar de manera constructiva las entradas, es hora de reevaluar su proceso de planificación de inventario.
Artículos Relacionados
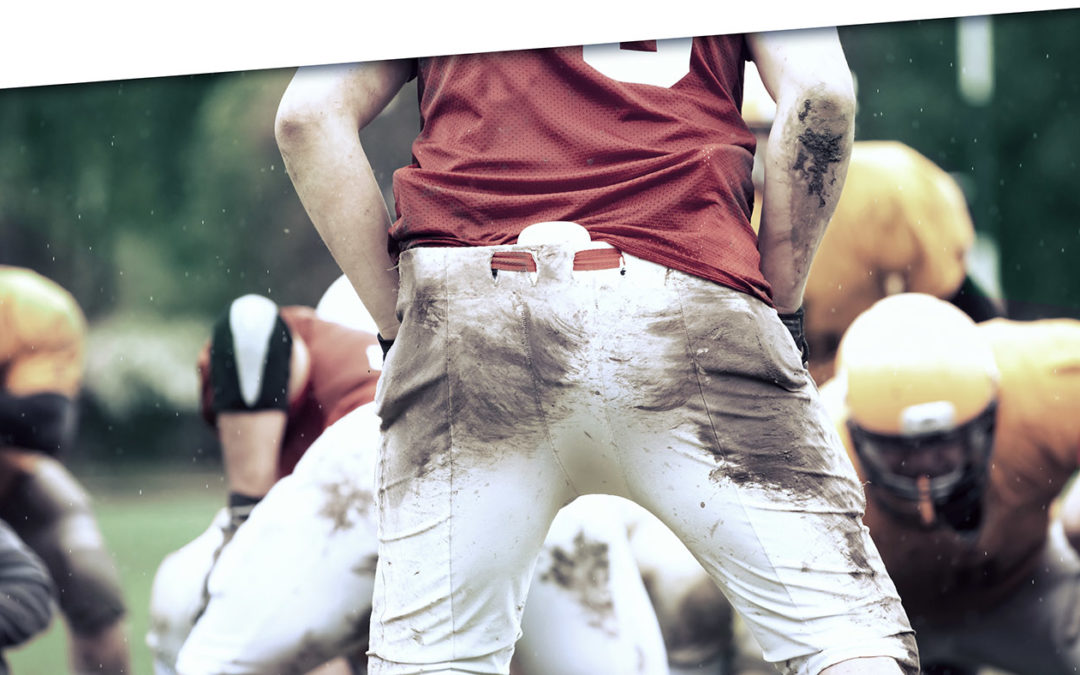
Una orden clara y concisa puede ayudar a contrarrestar de forma proactiva el ruido de la cadena de suministro
Usted ya conoce la situación: normalmente encuentra la mejor manera de administrar cada artículo del inventario calculando los puntos de pedido adecuados y los objetivos de reposición, pero luego se encuentra que la demanda promedioaumenta o disminuye , o cambia la volatilidad de la demanda, o cambian los tiempos de entrega de los proveedores, o cambian sus propios costos .
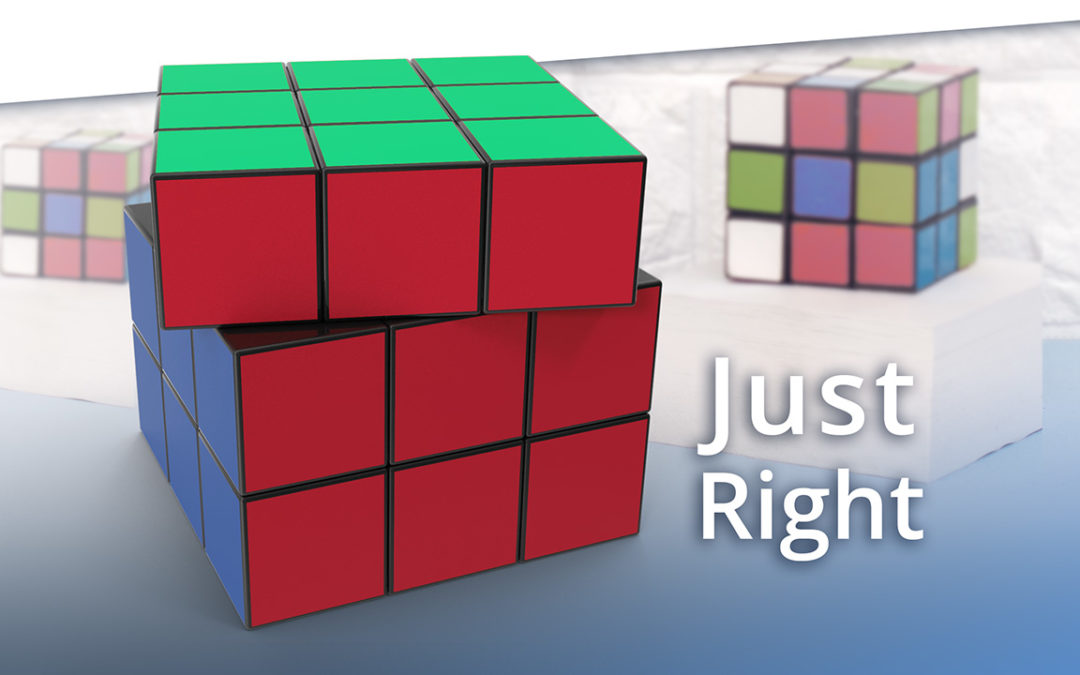
El cuento de Ricitos de Oro sobre los niveles de inventario
Puede que recuerdes la historia de Goldilocks de tu juventud hace mucho tiempo. A veces la papilla estaba demasiado caliente, a veces demasiado fría, pero solo una vez estaba bien. Ahora que somos adultos, podemos traducir ese cuento de hadas en un principio profesional para la planificación del inventario: puede haber muy poco o demasiado inventario, y hay un nivel de Ricitos de Oro que es “perfecto”. Este blog trata de encontrar ese punto dulce.
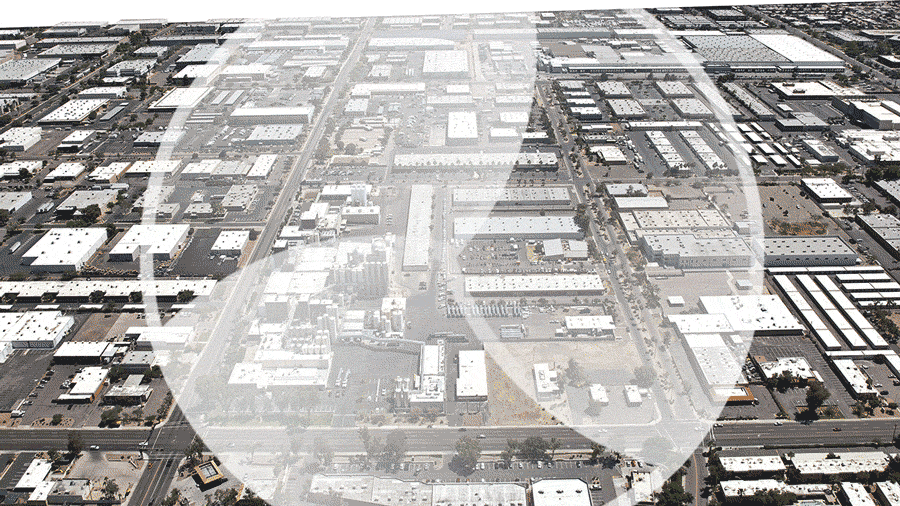
Ejemplos de optimización en Inventarios multi-escalón, basados en simulación
Administrar el inventario en múltiples instalaciones dispuestas en multi-escalón puede ser un gran desafío para cualquier empresa. La complejidad surge de las interacciones entre los escalones, con demandas en los niveles más bajos que aumentan y cualquier escasez en los niveles más altos se reduce en cascada.