De pandemie van Covid19 heeft ongebruikelijke druk gelegd op openbaarvervoersbedrijven. Deze stress dwingt agentschappen om opnieuw te kijken naar hun planningsprocessen voor reserveonderdelen, wat een belangrijke drijfveer is voor het waarborgen van uptime en het balanceren van de voorraadkosten van serviceonderdelen.
Deze blog richt zich op bussystemen en hun praktijken voor het beheer en de planning van reserveonderdelen. Er zijn hier echter lessen voor andere soorten openbaar vervoer, waaronder spoor en lightrail.
In 1995 publiceerde de Transportation Research Board (TRB) van de National Research Council een rapport dat nog steeds relevant is. Systeemspecifieke reservebusverhoudingen: een synthese van de transitpraktijk verklaarde:
Het doel van deze studie was het documenteren en onderzoeken van de kritieke locatiespecifieke variabelen die van invloed zijn op het aantal reservevoertuigen dat bussystemen nodig hebben om aan de maximale servicevereisten te voldoen. … Hoewel transitmanagers over het algemeen erkenden dat het juiste formaat van de vloot de operaties daadwerkelijk verbetert en de kosten verlaagt, meldden velen problemen bij het bereiken en consistent handhaven van een reserveratio van 20 procent, zoals aanbevolen door FTA… De respondenten van de enquête pleitten ervoor om meer nadruk te leggen op de ontwikkeling van verbeterde en innovatieve busonderhoudstechnieken, die hen zouden helpen de uitvaltijd te minimaliseren en de beschikbaarheid van voertuigen te verbeteren, wat uiteindelijk zou leiden tot minder reservevoertuigen en arbeids- en materiaalkosten.
Grof vereenvoudigde richtlijnen zoals "houd 20% reservebussen" zijn gemakkelijk te begrijpen en te meten, maar maskeren grovelijk meer gedetailleerde tactieken die een meer op maat gemaakt beleid kunnen bieden dat het geld van de belastingbetaler dat aan reserveonderdelen wordt uitgegeven, beter kan beheren en tegelijkertijd de hoogste niveaus van beschikbaarheid garandeert. Als de bedrijfszekerheid per bus kan worden verbeterd, zijn er minder reserveonderdelen nodig.
Een manier om elke bus vaker aan de praat te houden, is door het beheer van voorraden reserveonderdelen te verbeteren, met name door het gebruik van serviceonderdelen en het vereiste bevoorradingsbeleid nauwkeuriger te voorspellen. Hier kan modern supply chain management een belangrijke bijdrage leveren. De TRB merkte dit op in hun rapport:
Veel agentschappen zijn erin geslaagd de afhankelijkheid van overtollige reservevoertuigen te beperken. Die transitambtenaren zijn het erover eens dat verschillende factoren en initiatieven tot hun succes hebben geleid en van cruciaal belang zijn voor het succes van elk programma [inclusief] … Effectief gebruik van geavanceerde technologie om kritieke onderhoudsfuncties te beheren, inclusief de ordelijke en tijdige vervanging van onderdelen… Het niet beschikbaar hebben van service-onderdelen en andere componenten wanneer ze nodig zijn, heeft een negatieve invloed op elk onderhoudsprogramma.
Zolang managers op de hoogte zijn van de problemen en waakzaam zijn over welke hulpmiddelen voor hen beschikbaar zijn, zal de kans dat bussen 'geen voorraad hebben' sterk afnemen."
Effectief voorraadbeheer van reserveonderdelen vereist een balans tussen "genoeg hebben" en "te veel hebben". Wat moderne planningssoftware voor serviceonderdelen kan doen, is de wisselwerking tussen deze twee doelen zichtbaar maken, zodat transportmanagers op feiten gebaseerde beslissingen kunnen nemen over voorraden reserveonderdelen.
Er zijn genoeg complicaties bij het vinden van de juiste balans om verder te gaan dan simpele vuistregels zoals "houd tien dagen aan vraag bij de hand" of "bestel opnieuw wanneer u nog maar vijf stuks op voorraad hebt". Factoren die deze beslissingen sturen, zijn onder meer de gemiddelde vraag naar een onderdeel, de volatiliteit van die vraag, de gemiddelde doorlooptijd voor bevoorrading (wat een probleem kan zijn wanneer het onderdeel per slow boat uit Duitsland aankomt), de variabiliteit in doorlooptijd en verschillende kostenfactoren: aanhoudingskosten, bestelkosten en tekortkosten (bijv. verloren tarieven, verlies van publieke goodwill).
Innovatieve software voor supply chain-analyse en planning van reserveonderdelen maakt gebruik van geavanceerde probabilistische prognoses en stochastische optimalisatiemethoden om deze complexiteit te beheersen en een grotere beschikbaarheid van onderdelen tegen lagere kosten te bieden. Metro Transit in Minnesota documenteerde bijvoorbeeld een 4x hogere ROI in de eerste zes maanden na de implementatie van een nieuw systeem. Om meer te lezen over hoe openbaarvervoersbedrijven innovatieve supply chain-analyses benutten, zie:
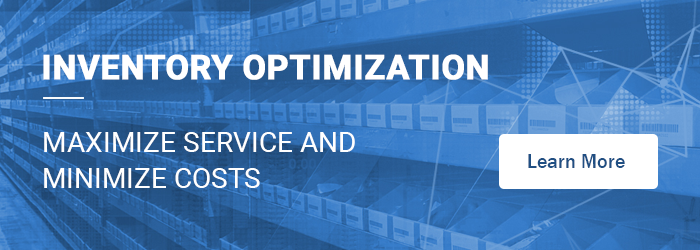