U kent de situatie: u berekent de beste manier om elk voorraadartikel te beheren door de juiste bestelpunten en aanvullingsdoelen te berekenen, vervolgens de gemiddelde vraag stijgt of daalt, of de vraagvolatiliteit verandert, of de doorlooptijden van leveranciers veranderen, of uw eigen kosten veranderen . Nu zijn uw oude polissen (herbestelpunten, veiligheidsvoorraden, Min/Max-niveaus, enz.) achterhaald - net op het moment dat u denkt dat u ze goed heeft. Door gebruik te maken van geavanceerde software voor planning en voorraadoptimalisatie, kunt u proactief inspelen op de steeds veranderende invloeden van buitenaf op uw voorraad en vraag. Om dit te doen, moet u de voorraadparameters regelmatig opnieuw kalibreren op basis van de steeds veranderende vraag en doorlooptijden.
Onlangs hebben enkele potentiële klanten hun bezorgdheid geuit dat door regelmatig de parameters voor voorraadbeheer te wijzigen, ze "ruis" introduceren en complicaties toevoegen aan hun activiteiten. Een bezoeker van onze stand op de Microsoft Dynamics User Group Conference van vorige week merkte op:
“We willen de operaties niet in de war sturen door het beleid te vaak te veranderen en ruis in het systeem te introduceren. Dat geluid maakt het systeem nerveus en zorgt voor verwarring bij het inkoopteam.”
Deze visie is gebaseerd op de paradigma's van gisteren. Hoewel u over het algemeen een onmiddellijke productierun niet moet wijzigen, zal het negeren van wijzigingen op korte termijn in het beleid dat de toekomstige productieplanning en orderaanvulling stuurt, grote schade aanrichten aan uw activiteiten. Of je het nu leuk vindt of niet, de ruis is er al in de vorm van extreme vraag en variabiliteit in de toeleveringsketen. Door aanvullingsparameters vast te stellen, ze niet vaak bij te werken of alleen te beoordelen op het moment van bestelling, kan uw Supply Chain Operations alleen op problemen reageren in plaats van ze proactief te identificeren en corrigerende maatregelen te nemen.
Het aanpassen van het beleid met herkalibraties op korte termijn is aanpassen aan een veranderlijke situatie in plaats van eraan vast te zitten. We kunnen kijken naar de NFL-games van afgelopen weekend voor een eenvoudige analogie. Stelt u zich eens voor dat de quarterback van uw favoriete team consequent weigert een hoorbare te roepen (wijzig het spel net voordat de bal wordt geknapt) nadat hij de verdedigende formatie heeft gezien. Dit zou resulteren in veel gemiste kansen, inefficiëntie en vastgelopen ritten die het team een overwinning zouden kunnen kosten. Wat zou je willen dat je quarterback doet?
Vraag, doorlooptijden, kosten en zakelijke prioriteiten veranderen vaak, en zoals de afgelopen 18 maanden hebben bewezen, veranderen ze vaak aanzienlijk. Als Supply Chain-leider heeft u de keuze: parameters vast houden, wat resulteert in een groot aantal razendsnelle versnellingen en orderannuleringen, of proactief de parameters voor voorraadbeheer wijzigen. Het hoorbare oproepen door uw beleid opnieuw te kalibreren als vraag- en aanbodsignalen veranderen, is de juiste zet.
Hier is een voorbeeld. Stel dat u een kritiek artikel beheert door het bestelpunt (ROP) op 25 eenheden en de bestelhoeveelheid (OQ) op 48 te regelen. U voelt zich misschien een rots van stabiliteit door aan die twee nummers vast te houden, maar door dit te doen, kunt u andere getallen dramatisch laten fluctueren. Met name uw toekomstige serviceniveaus, opvullingspercentages en bedrijfskosten zouden allemaal uit het zicht kunnen worden gereset terwijl u zich fixeert op het vasthouden aan de ROP en OQ van gisteren. Toen het beleid oorspronkelijk werd vastgesteld, was de vraag stabiel en waren de doorlooptijden voorspelbaar, wat een serviceniveau van 99% op een belangrijk item opleverde. Maar nu neemt de vraag toe en zijn de doorlooptijden langer. Verwacht je echt hetzelfde resultaat (99%-serviceniveau) met dezelfde input-sets nu vraag en doorlooptijden zo verschillend zijn? Natuurlijk niet. Stel dat u wist dat u, gezien de recente veranderingen in vraag en doorlooptijd, de ROP moest verhogen tot 35 eenheden om hetzelfde serviceniveaudoel van 99% te bereiken. Als u de ROP op 25 eenheden zou houden, zou uw serviceniveau dalen tot 92%. Is het beter om dit van tevoren te weten of om gedwongen te worden om te reageren als u te maken heeft met stockouts?
Wat software voor voorraadoptimalisatie en -planning doet, is de verbanden tussen prestatiestatistieken zoals servicesnelheid en controleparameters zoals ROP en ROQ zichtbaar maken. Het onzichtbare wordt zichtbaar, zodat u beredeneerde aanpassingen kunt maken die uw statistieken houden waar u ze nodig hebt door de bedieningshendels aan te passen die beschikbaar zijn voor uw gebruik. Door probabilistische prognosemethoden te gebruiken, kunt u Key Performance Predictions (KPP's) van prestaties en kosten genereren, terwijl u corrigerende acties op korte termijn identificeert, zoals gerichte voorraadbewegingen die problemen helpen voorkomen en kansen benutten. Als u dit niet doet, komt uw supply chain-planning in een keurslijf terecht, net zoals de quarterback die weigert te horen.
Toegegeven, een voortdurend veranderende zakelijke omgeving vereist constante waakzaamheid en af en toe een reactie. Maar de juiste software voor voorraadoptimalisatie en vraagvoorspelling kan uw controleparameters met een paar muisklikken op schaal herberekenen en uw ERP-systeem aanwijzingen geven hoe alles op koers te houden ondanks de constante turbulentie. De ruis zit al in uw systeem in de vorm van vraag- en aanbodvariabiliteit. Ga je proactief hoorbaar of vasthouden aan een ouder plan en duimen dat het goed komt?
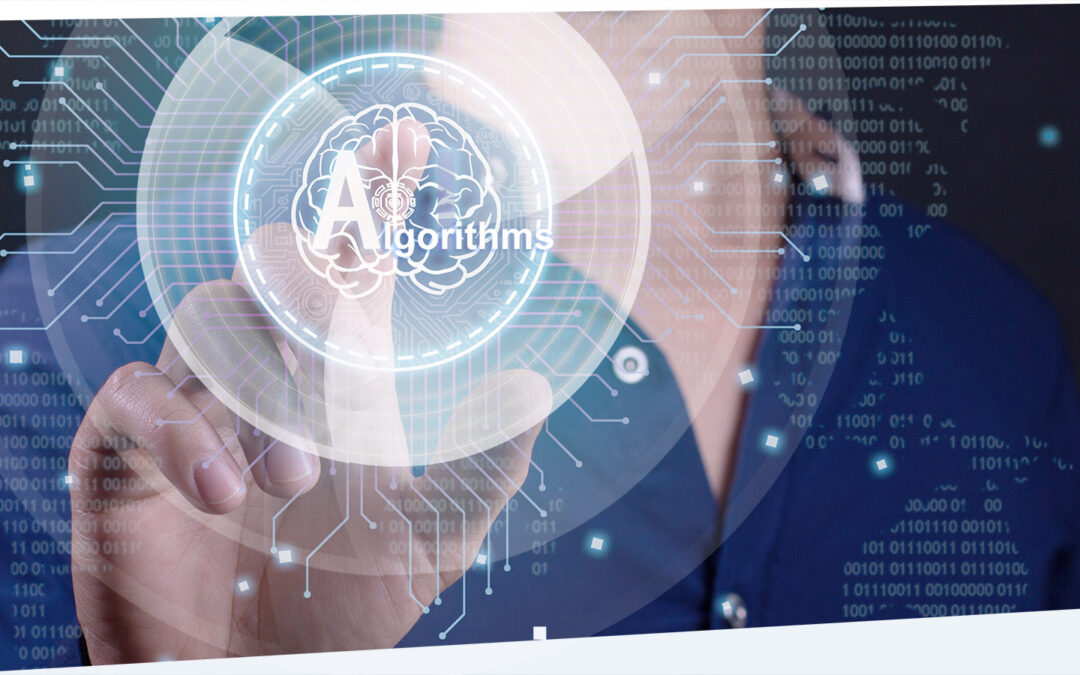
Je moet samenwerken met de algoritmen
Dit artikel gaat over de echte kracht die voortkomt uit de samenwerking tussen u en onze software die binnen handbereik plaatsvindt. We schrijven vaak over de software zelf en wat er ‘onder de motorkap’ gebeurt. Deze keer is het onderwerp hoe je het beste met de software kunt samenwerken.
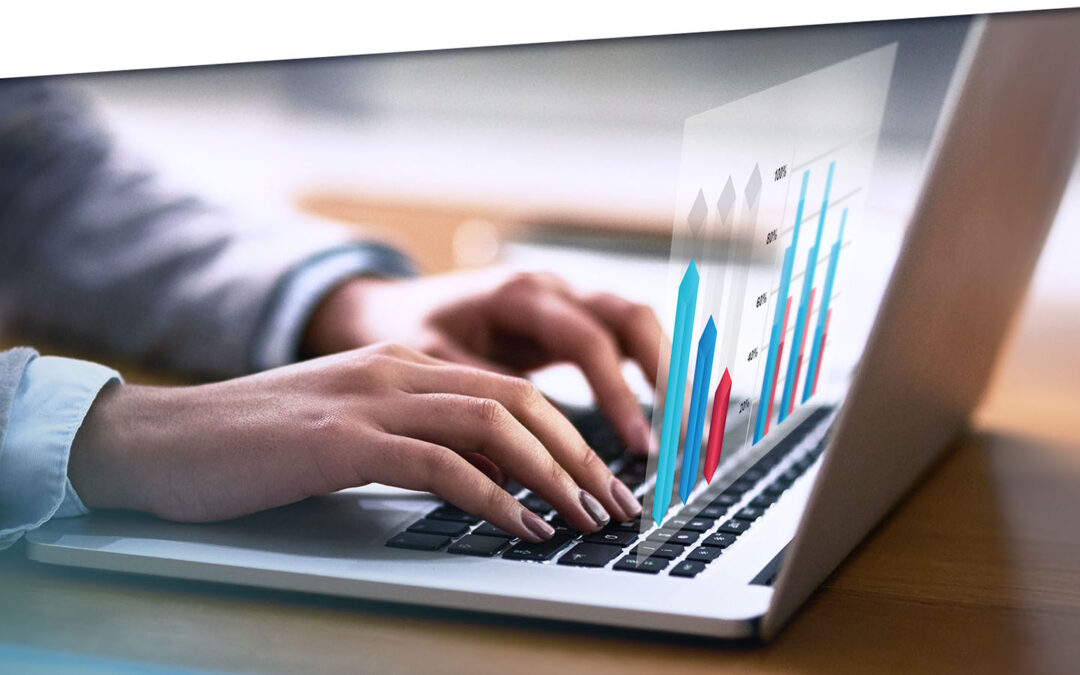
Het gebruik van belangrijke prestatievoorspellingen om het voorraadbeleid te plannen
Ik kan me niet voorstellen dat ik een voorraadplanner ben op het gebied van reserveonderdelen, distributie of productie en dat ik veiligheidsvoorraden, bestelpunten en bestelsuggesties moet creëren zonder gebruik te maken van belangrijke prestatievoorspellingen van serviceniveaus, opvullingspercentages en voorraadkosten.
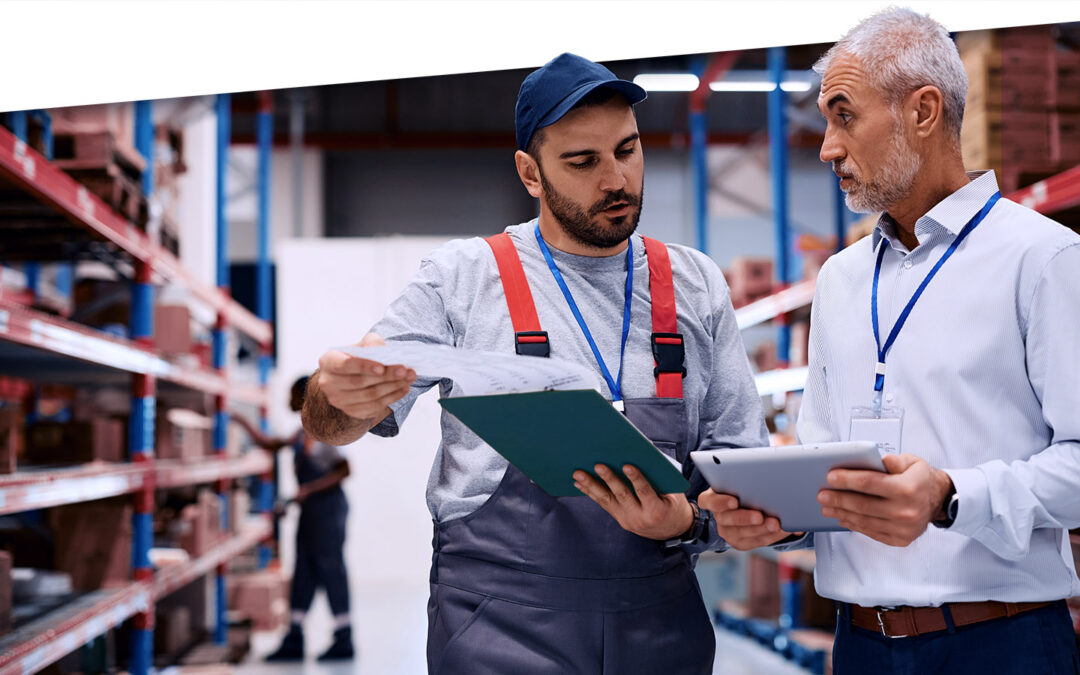
Belangrijkste verschillen tussen voorraadplanning voor eindproducten en voor MRO en reserveonderdelen
In het huidige competitieve zakelijke landschap zijn bedrijven voortdurend op zoek naar manieren om hun operationele efficiëntie te verbeteren en meer inkomsten te genereren. Het optimaliseren van het beheer van serviceonderdelen is een vaak over het hoofd gezien aspect dat een aanzienlijke financiële impact kan hebben. Bedrijven kunnen de algehele efficiëntie verbeteren en aanzienlijke financiële opbrengsten genereren door de voorraad reserveonderdelen effectief te beheren. Dit artikel gaat in op de economische implicaties van geoptimaliseerd beheer van serviceonderdelen en hoe investeren in software voor voorraadoptimalisatie en vraagplanning een concurrentievoordeel kan opleveren.