In een zeer configureerbare productieomgeving kan het voorspellen van eindproducten een complexe en lastige taak worden. Het aantal mogelijke eindproducten schiet omhoog als veel componenten uitwisselbaar zijn. Een traditionele MRP zou ons dwingen om elk eindproduct te voorspellen, wat onrealistisch of zelfs onmogelijk kan zijn. Verschillende toonaangevende oplossingen introduceren het concept van de “Planning BOM”, waarmee prognoses op een hoger niveau in het productieproces kunnen worden gebruikt. In dit artikel bespreken we deze functionaliteit in Epicor Kinetic en hoe u hiervan kunt profiteren met Epicor Smart Inventory Planning and Optimization (Smart IP&O) om uw vraag voor te blijven in het licht van deze complexiteit.
Waarom heb ik een planningsstuklijst nodig?
Traditioneel zou elk eindproduct of elke SKU een strak gedefinieerde stuklijst hebben. Als we dat product op voorraad hebben en rond de voorspelde vraag willen plannen, zullen we de vraag naar die producten voorspellen en vervolgens MRP invoeren om deze voorspelde vraag via de stuklijst van het niveau van het eindproduct naar de componenten te blazen.
Veel bedrijven bieden echter zeer configureerbare producten aan waarbij klanten opties kunnen selecteren voor het product dat ze kopen. Denk bijvoorbeeld eens aan de laatste keer dat u een mobiele telefoon kocht. Je hebt een merk en model gekozen, maar van daaruit kreeg je waarschijnlijk opties voorgeschoteld: welk schermformaat wil je? Hoeveel opslagruimte wil je? Welke kleur heeft jouw voorkeur? Als dat bedrijf deze mobiele telefoons binnen een redelijke termijn klaar en beschikbaar wil hebben om naar u te verzenden, anticiperen ze plotseling niet langer alleen maar op de vraag naar dat model; ze moeten dat model voorspellen voor elk type schermformaat, voor alle opslagcapaciteiten, voor alle kleuren, en ook voor alle mogelijke combinaties daarvan! Voor sommige fabrikanten kunnen deze configuraties honderden of duizenden mogelijke voltooide goede permutaties opleveren.
Er kunnen zoveel aanpassingen mogelijk zijn dat de vraag op het niveau van het eindproduct in traditionele zin volkomen onvoorspelbaar is. Duizenden van deze mobiele telefoons kunnen elk jaar worden verkocht, maar voor elke mogelijke configuratie kan de vraag extreem laag en sporadisch zijn – misschien worden bepaalde combinaties één keer verkocht en nooit meer.
Dit dwingt deze bedrijven vaak om bestelpunten en veiligheidsvoorraadniveaus vooral op componentniveau te plannen, terwijl ze grotendeels reageren op de sterke vraag op het niveau van eindproducten via MRP. Hoewel dit een geldige aanpak is, ontbreekt het aan een systematische manier om voorspellingen te doen die rekening kunnen houden met verwachte toekomstige activiteiten, zoals promoties, aanstaande projecten of verkoopkansen. Voorspellen op het 'geconfigureerde' niveau is feitelijk onmogelijk, en het is ook niet haalbaar om deze prognoseaannames op componentniveau te verweven.
Planning BOM uitgelegd Hier komen Planning BOM's om de hoek kijken. Misschien werkt het verkoopteam aan een grote B2B-mogelijkheid voor dat model, of is er een geplande promotie voor Cyber Monday. Hoewel het niet realistisch is om met deze aannames voor elke mogelijke configuratie te werken, is het op modelniveau wel heel goed te doen – en enorm waardevol.
De Planningsstuklijst kan een prognose op een hoger niveau gebruiken en vervolgens de vraag naar beneden blazen op basis van vooraf gedefinieerde verhoudingen voor de mogelijke componenten ervan. De fabrikant van mobiele telefoons weet bijvoorbeeld misschien dat de meeste mensen kiezen voor 128 GB opslagruimte, en dat veel minder mensen kiezen voor upgrades naar 256 GB of 512 GB. Met de planningsstuklijst kan de organisatie (bijvoorbeeld) 60% van de vraag terugbrengen naar de 128GB-optie, 30% naar de 256GB-optie en 10% naar de 512GB-optie. Ze zouden hetzelfde kunnen doen voor schermformaten, kleuren of andere beschikbare aanpassingen.
Het bedrijf kan zijn prognose nu op dit modelniveau richten, waarbij de planningsstuklijst de componentenmix bepaalt. Het is duidelijk dat het definiëren van deze verhoudingen enige aandacht vergt, maar het plannen van stuklijsten stelt bedrijven in staat te voorspellen wat anders onvoorspelbaar zou zijn.
Het belang van een goede voorspelling
Natuurlijk hebben we nog steeds een goede voorspelling nodig om in Epicor Kinetic te laden. Zoals uitgelegd in dit artikel, kan Epicor Kinetic weliswaar een voorspelling importeren, maar kan het er vaak geen genereren, en als dat wel het geval is, zijn er vaak een groot aantal moeilijk te gebruiken configuraties nodig die niet vaak opnieuw worden bezocht, wat resulteert in onnauwkeurige prognoses. . Het is daarom aan het bedrijf om met zijn eigen sets prognoses te komen, vaak handmatig geproduceerd in Excel. Handmatige prognoses brengen over het algemeen een aantal uitdagingen met zich mee, waaronder maar niet beperkt tot:
- Het onvermogen om vraagpatronen zoals seizoensinvloeden of trends te identificeren.
- Overmatig vertrouwen op klant- of verkoopprognoses.
- Gebrek aan nauwkeurigheid of prestatieregistratie.
Hoe goed de MRP ook is geconfigureerd met uw zorgvuldig overwogen planningsstuklijsten, een slechte prognose betekent een slechte MRP-output en wantrouwen in het systeem: garbage in, garbage out. Als we verdergaan met het voorbeeld van het ‘mobiele telefoonbedrijf’, zonder een systematische manier om de belangrijkste vraagpatronen en/of domeinkennis in de prognose vast te leggen, kan MRP dit nooit zien.
Slimme IP&O: een allesomvattende oplossing
Smart IP&O ondersteunt planning op alle niveaus van uw stuklijst, hoewel het “uitblazen” wordt afgehandeld via MRP binnen Epicor Kinetic. Dit is de methode die we gebruiken voor onze Epicor Kinetic-klanten, die eenvoudig en effectief is:
- Smart Demand Planner: Het platform bevat een speciaal gebouwde prognosetoepassing genaamd Smart Demand Planner die u gaat gebruiken om de vraag naar uw vervaardigde producten (meestal eindproducten) te voorspellen. Het genereert statistische prognoses, stelt planners in staat aanpassingen aan te brengen en/of andere prognoses in te passen (zoals verkoop- of klantprognoses) en houdt de nauwkeurigheid bij. De output hiervan is een prognose die wordt ingevoerd in de prognoseinvoer in Epicor Kinetic, waar MRP deze zal ophalen. MRP zal vervolgens gebruik maken van de vraag op het niveau van het eindproduct en ook de materiaalvereisten via de stuklijst uitblazen, zodat de vraag ook op lagere niveaus wordt onderkend.
- Smart Inventory Optimization: U gebruikt tegelijkertijd Smart Inventory Optimization om min-/max-/veiligheidsniveaus in te stellen voor zowel alle eindproducten die u op voorraad maakt (indien van toepassing; sommige van onze klanten werken puur op bestelling op basis van een vaste vraag), als voor onbewerkte goederen materialen. De sleutel hier is dat Smart op grondstofniveau de vraag naar werkgebruik, doorlooptijden van leveranciers, enz. zal benutten om deze parameters te optimaliseren, terwijl tegelijkertijd verkooporders/verzendingen worden gebruikt als vraag op het niveau van het eindproduct. Smart verwerkt deze meerdere inputs van de vraag op elegante wijze via de bidirectionele integratie met Epicor Kinetic.
Wanneer MRP wordt uitgevoerd, worden vraag en aanbod (wat wederom de vraag naar grondstoffen omvat die voortvloeit uit de voltooide goede prognose) geneutraliseerd met de min/max/veiligheidsniveaus die u hebt vastgesteld om PO- en werksuggesties voor te stellen.
Breid Epicor Kinetic uit met Smart IP&O
Smart IP&O is ontworpen om uw Epicor Kinetic-systeem uit te breiden met vele geïntegreerde oplossingen voor vraagplanning en voorraadoptimalisatie. Het kan bijvoorbeeld automatisch statistische prognoses genereren voor grote aantallen artikelen, maakt intuïtieve prognoseaanpassingen mogelijk, houdt de nauwkeurigheid van prognoses bij en stelt u uiteindelijk in staat echte op consensus gebaseerde prognoses te genereren om beter te kunnen anticiperen op de behoeften van uw klanten.
Dankzij de zeer flexibele producthiërarchieën is Smart IP&O perfect geschikt voor prognoses op het niveau van de Planning BOM, zodat u belangrijke patronen kunt vastleggen en bedrijfskennis kunt integreren op de niveaus die er het meest toe doen. Bovendien kunt u op elk niveau van uw stuklijst optimale veiligheidsvoorraden analyseren en inzetten.
Door gebruik te maken van de Planning BOM-mogelijkheden van Epicor Kinetic naast de geavanceerde functies voor prognoses en voorraadoptimalisatie van Smart IP&O, zorgt u ervoor dat u efficiënt en nauwkeurig aan de vraag kunt voldoen, ongeacht de complexiteit van uw productconfiguraties. Deze synergie verbetert niet alleen de nauwkeurigheid van de prognoses, maar versterkt ook de algehele operationele efficiëntie, waardoor u voorop kunt blijven lopen in een concurrerende markt.
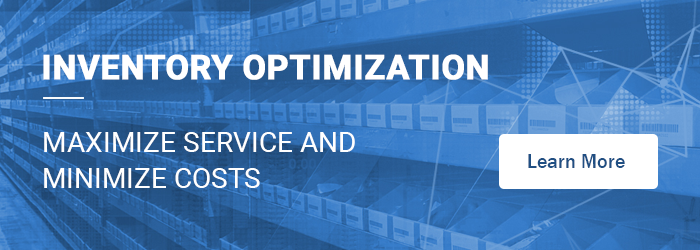