Of u nu 'Min/Max' of 'bestelpunt' en 'bestelhoeveelheid' gebruikt om te bepalen wanneer en hoeveel u moet bijvullen, uw aanpak kan enorme efficiëntie opleveren of juist niet. Belangrijkste fouten om te vermijden:
- Niet regelmatig opnieuw kalibreren
- Min/Max alleen bekijken als er een probleem is
- Het gebruik van prognosemethoden voldoet niet aan de taak
- Ervan uitgaande dat gegevens te traag of onvoorspelbaar zijn om er toe te doen
“We hebben meer dan 150.000 combinaties van SKU x locatie. Onze vraag is intermitterend. Omdat het langzaam gaat, hoeven we onze bestelpunten niet vaak opnieuw te berekenen. We doen dit misschien één keer per jaar, maar we bekijken de bestelpunten wanneer er een probleem is.” - Materiaalbeheerder.
Deze reactieve benadering zal leiden tot miljoenen overtollige voorraden, voorraadtekorten en veel tijdverspilling bij het beoordelen van gegevens wanneer 'er iets misgaat'. Toch heb ik in de loop der jaren van zoveel voorraadprofessionals ditzelfde afzien gehoord. Het is duidelijk dat we meer moeten doen om te delen waarom dit denken zo problematisch is.
Het is waar dat voor veel onderdelen een herberekening van de bestelpunten met up-to-date historische gegevens en doorlooptijden niet veel zal veranderen, vooral als patronen zoals trend of seizoensinvloeden niet aanwezig zijn. Veel onderdelen hebben echter baat bij een herberekening, vooral als de doorlooptijden of de recente vraag zijn veranderd. Bovendien neemt de kans op een significante wijziging die een herberekening noodzakelijk maakt, toe naarmate u langer wacht. Ten slotte hebben die maanden zonder eisen ook invloed op de kansen en mogen niet ronduit worden genegeerd. Het belangrijkste punt is echter dat het onmogelijk is om te weten wat er wel of niet zal veranderen in uw prognose, dus het is beter om regelmatig opnieuw te kalibreren.
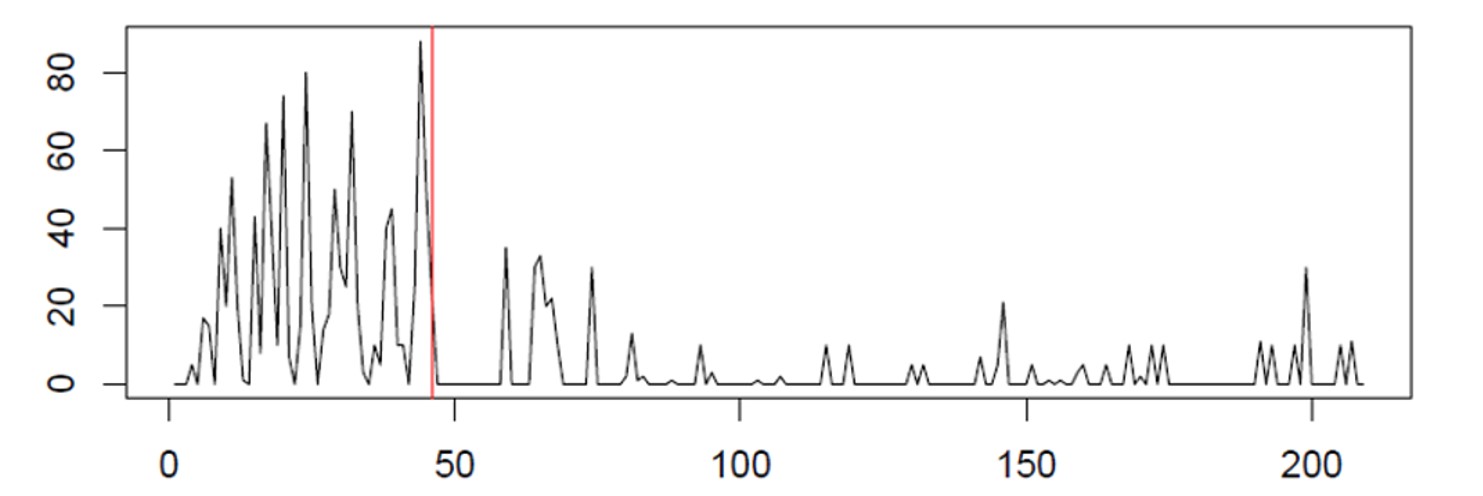
Deze opvallende casus uit gegevens uit de echte wereld illustreert een scenario waarin regelmatige en geautomatiseerde herkalibratie uitblinkt: de voordelen van snelle reacties op veranderende vraagpatronen zoals deze tellen snel op. In het bovenstaande voorbeeld vertegenwoordigt de X-as dagen en vertegenwoordigt de Y-as de vraag. Als u enkele maanden zou moeten wachten tussen het opnieuw kalibreren van uw bestelpunten, zou u ongetwijfeld veel te vroeg bestellen. Door uw bestelpunt veel vaker opnieuw te kalibreren, vangt u de verandering in de vraag op, waardoor u veel nauwkeuriger kunt bestellen.
In plaats van te wachten tot u een probleem hebt, kunt u alle onderdelen elke planningscyclus minstens één keer per maand opnieuw kalibreren. Hierdoor wordt gebruik gemaakt van de nieuwste gegevens en wordt het voorraadbeleid proactief aangepast, waardoor problemen worden vermeden die handmatige controles en voorraadtekorten of -overschotten zouden veroorzaken.
De aard van uw (potentieel gevarieerde) gegevens moet ook worden gekoppeld aan de juiste prognosetools. Als records voor sommige onderdelen trend- of seizoenspatronen laten zien, kan het gebruik van targetingprognosemethoden om deze patronen te accommoderen een groot verschil maken. Evenzo, als de gegevens frequente nulwaarden laten zien (intermitterende vraag), kunnen voorspellingsmethoden die niet rond dit speciale geval zijn gebouwd, gemakkelijk onbetrouwbare resultaten opleveren.
Automatiseer, herkalibreer en bekijk uitzonderingen. Speciaal gebouwde software doet dit automatisch. Zie het op een andere manier: is het beter om eenmaal per jaar een hoop geld in uw 401K te storten of "dollarkostengemiddelde" door het hele jaar door kleinere, even grote bedragen te storten. Het regelmatig opnieuw kalibreren van beleid zal in de loop van de tijd een maximaal rendement opleveren, net zoals dollar cost avering dat zal doen voor uw beleggingsportefeuille.
Hoe vaak herijkt u uw voorraadbeleid opnieuw? Waarom?