La pandemia de Covid19 ha puesto un estrés inusual en las agencias de transporte público. Este estrés obliga a las agencias a revisar nuevamente sus procesos de planificación de piezas de repuesto, que es un factor clave para garantizar el tiempo de actividad y equilibrar los costos de inventario de piezas de servicio.
Este blog se centra en los sistemas de autobuses y sus prácticas para la gestión y planificación de piezas de repuesto. Sin embargo, aquí hay lecciones para otros tipos de transporte público, incluidos el tren y el tren ligero.
En 1995, la Junta de Investigación del Transporte (TRB) del Consejo Nacional de Investigación publicó un informe que aún tiene relevancia. Proporciones de autobuses de repuesto específicas del sistema: una síntesis de la práctica de tránsito fijado
El propósito de este estudio fue documentar y examinar las variables críticas específicas del sitio que afectan la cantidad de vehículos de repuesto que los sistemas de autobuses necesitan para mantener los requisitos máximos de servicio. … Si bien los gerentes de tránsito generalmente reconocieron que dimensionar correctamente la flota en realidad mejora las operaciones y reduce los costos, muchos informaron dificultades para lograr y mantener de manera constante una proporción de repuesto del 20 por ciento, como recomienda la FTA… Quienes respondieron a la encuesta abogaron por que se ponga más énfasis en el desarrollo de técnicas de mantenimiento de autobuses mejoradas e innovadoras, que los ayudarían a minimizar el tiempo de inactividad y mejorar la disponibilidad de los vehículos, lo que finalmente conduciría a vehículos de repuesto reducidos y costos de mano de obra y materiales.
Las pautas sumamente simplificadas como "mantener los autobuses de repuesto 20%" son fáciles de entender y medir, pero enmascaran tácticas más detalladas que pueden proporcionar políticas más personalizadas que administren mejor el dinero de los contribuyentes gastado en repuestos al tiempo que garantizan los más altos niveles de disponibilidad. Si se puede mejorar la confiabilidad operativa para cada bus, se necesitarán menos repuestos.
Una forma de mantener cada autobús en funcionamiento con más frecuencia es mejorar la gestión de los inventarios de piezas de repuesto, específicamente pronosticando el uso de piezas de servicio y las políticas de reabastecimiento requeridas con mayor precisión. Aquí es donde la gestión moderna de la cadena de suministro puede hacer una contribución significativa. El TRB señaló esto en su informe:
Muchas agencias han logrado limitar la dependencia del exceso de vehículos de repuesto. Esos funcionarios de tránsito están de acuerdo en que varios factores e iniciativas han llevado a su éxito y son fundamentales para el éxito de cualquier programa [incluido] … Uso eficaz de tecnología avanzada para gestionar funciones críticas de mantenimiento, incluido el reemplazo ordenado y oportuno de piezas… La falta de disponibilidad de piezas de repuesto y otros componentes cuando se necesitan afectará negativamente cualquier programa de mantenimiento.
Siempre que los gerentes sean conscientes de los problemas y estén atentos a las herramientas disponibles para ellos, la probabilidad de que los autobuses se queden sin existencias disminuirá considerablemente”.
La gestión eficaz del inventario de piezas de repuesto requiere un equilibrio entre "tener suficiente" y "tener demasiado". Lo que puede hacer el software moderno de planificación de piezas de servicio es hacer visible la compensación entre estos dos objetivos para que los gerentes de tránsito puedan tomar decisiones basadas en hechos sobre los inventarios de piezas de repuesto.
Hay suficientes complicaciones para encontrar el equilibrio adecuado como para requerir ir más allá de las reglas generales simples como "mantener a mano la demanda de diez días" o "volver a pedir cuando tenga menos de cinco unidades en stock". Los factores que impulsan estas decisiones incluyen tanto la demanda promedio de una pieza, la volatilidad de esa demanda, el tiempo promedio de reabastecimiento (que puede ser un problema cuando la pieza llega en un barco lento desde Alemania), la variabilidad en el tiempo de entrega y varios factores de costo: costos de mantenimiento, costos de pedidos y costos de escasez (p. ej., tarifas perdidas, pérdida de buena voluntad pública).
El innovador software de planificación de piezas de repuesto y análisis de la cadena de suministro utiliza métodos avanzados de predicción probabilística y optimización estocástica para gestionar estas complejidades y proporcionar una mayor disponibilidad de piezas a un costo menor. Por ejemplo, Metro Transit de Minnesota documentó un aumento de 4 veces en el retorno de la inversión en los primeros seis meses de implementación de un nuevo sistema. Para obtener más información sobre cómo las agencias de transporte público están explotando los análisis innovadores de la cadena de suministro, consulte:
- Optimización en la gestión de piezas en BC Transit
- Software inteligente y Metro Transit
- El software inteligente ayuda a Metro-North Railroad a mantener los trenes funcionando a tiempo
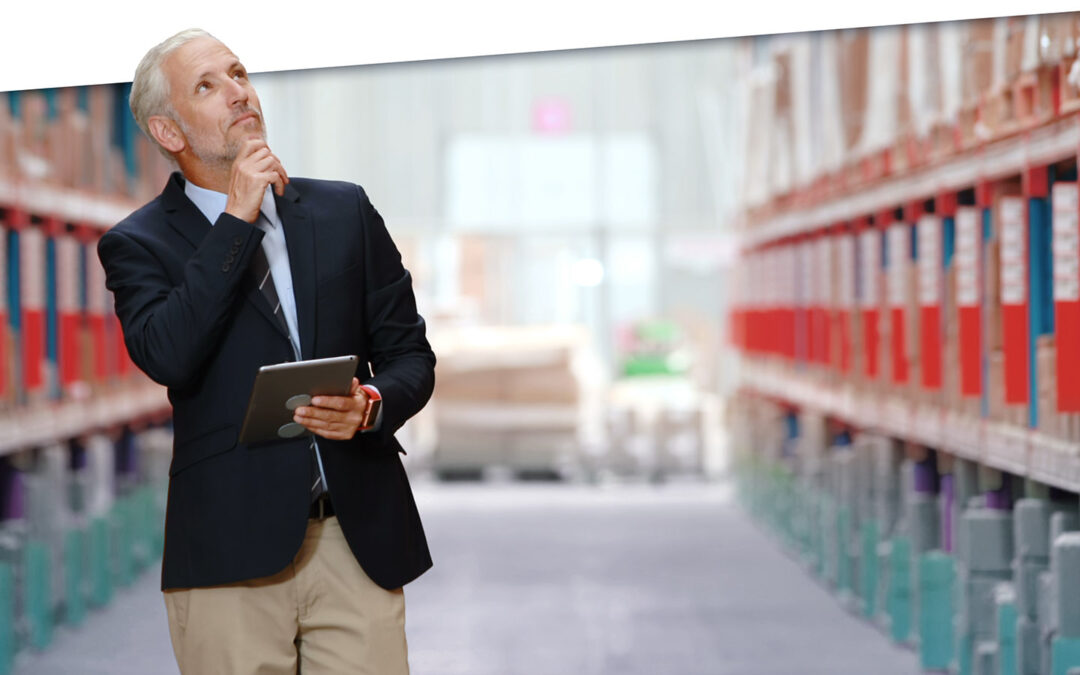
Por qué la planificación del inventario no debería depender exclusivamente de reglas generales simples
Para demasiadas empresas, una pieza fundamental de la investigación de datos –la medición de la incertidumbre de la demanda– se maneja mediante reglas generales simples pero inexactas. Por ejemplo, los planificadores de la demanda a menudo calculan el stock de seguridad mediante un múltiplo definido por el usuario del pronóstico o promedio histórico. O pueden configurar su ERP para pedir más cuando el inventario disponible llegue a 2 veces la demanda promedio durante el tiempo de entrega para artículos importantes y 1,5 veces para los menos importantes. Este es un gran error con costosas consecuencias.
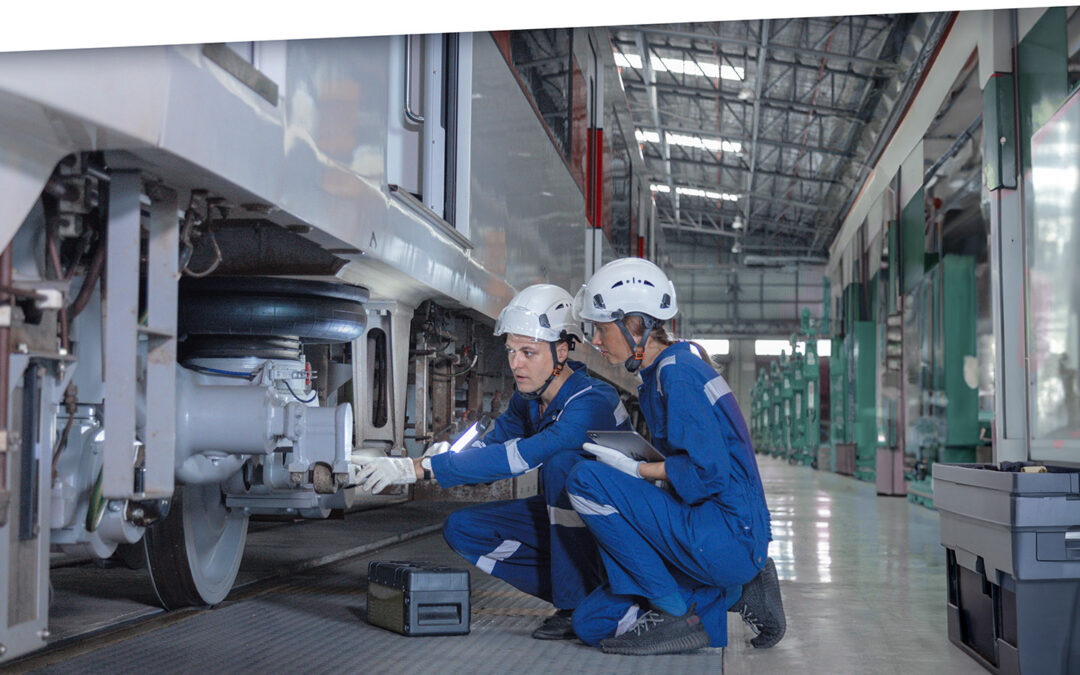
Por qué las empresas de MRO deberían preocuparse por el exceso de inventario
¿Las empresas de MRO realmente priorizan la reducción del exceso de inventario de repuestos? Desde un punto de vista organizativo, nuestra experiencia sugiere que no necesariamente. Las discusiones en las salas de juntas generalmente giran en torno a la expansión de flotas, la adquisición de nuevos clientes, el cumplimiento de acuerdos de nivel de servicio (SLA), la modernización de la infraestructura y la maximización del tiempo de actividad. En industrias donde los activos respaldados por repuestos cuestan cientos de millones o generan ingresos significativos (por ejemplo, minería o petróleo y gas), el valor del inventario simplemente no sorprende y las organizaciones tienden a pasar por alto cantidades masivas de inventario excesivo.
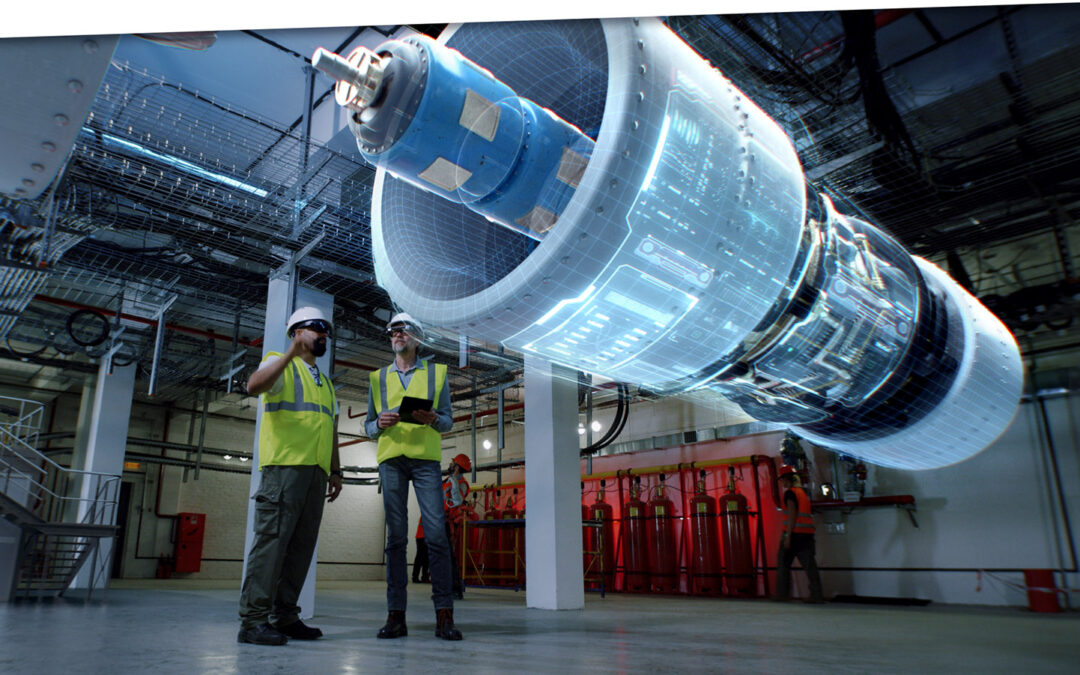
Juego constructivo con gemelos digitales
Aquellos de ustedes que siguen temas candentes estarán familiarizados con el término "gemelo digital". Aquellos que han estado demasiado ocupados con el trabajo tal vez quieran seguir leyendo y ponerse al día. Si bien existen varias definiciones de gemelo digital, aquí hay una que funciona bien: un gemelo digital es una copia virtual dinámica de un activo físico, proceso, sistema o entorno que se parece y se comporta de manera idéntica a su contraparte del mundo real. Un gemelo digital ingiere datos y replica procesos para que pueda predecir posibles resultados de rendimiento y problemas que podría experimentar el producto del mundo real.